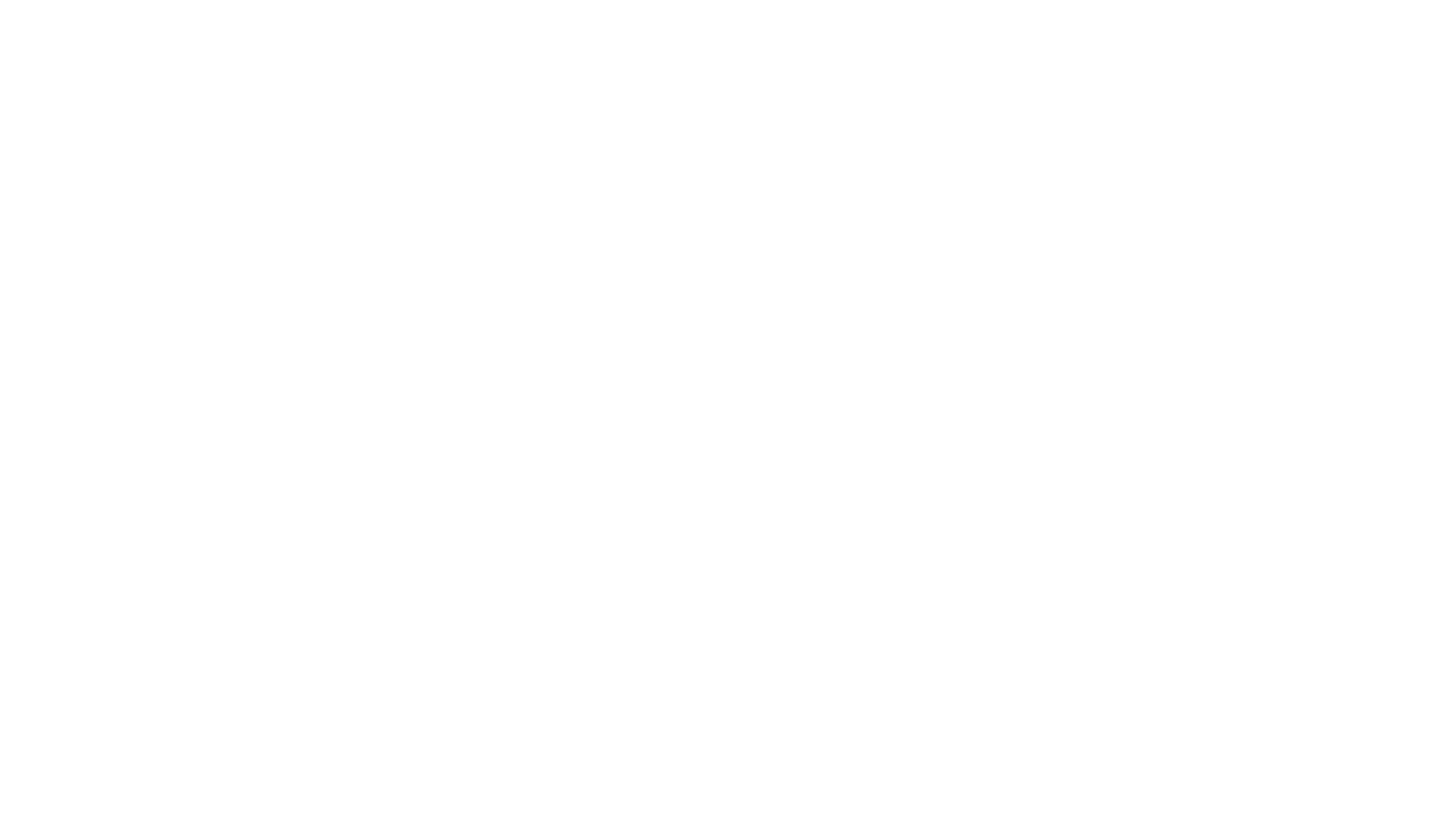
KIRO Fill
Automated Compounding Device for Sterile Non-Hazardous Preparations
Features
Material Preparation and Identification Area
- Touchscreen for user instructions and confirmations
- Barcode/datamatrix and radio frequency identification (RFID) systems to identify and control source and final containers used
Loading/Unloading Area
- Manual loading and unloading
- Barcode scanning of raw materials
- RFID technology for in process tracking
- Up to 20 loading positions for final syringes (including 3 mL, 5 mL, 10 mL, 20 mL, 30 mL, and 60 mL)
- Source bags and vials of different brands and sizes supported
- LED-guided positioning
Compounding Area
- Two automated units working in parallel handle transfer syringes to withdraw solutions from source containers and fill syringes via luer lock connections
- Automatic capping of syringes with tamper-evident caps
- Control of used source containers and drug leftovers
Air Treatment Area
- ISO 5 aseptic environment in material preparation, loading, and unloading areas and in lower compounding area
- Horizontal air flow with high efficiency particulate air (HEPA) H14 filters
- Continuous monitoring of:
– Air flow operation
– Non-viable particle counts
– Temperature
WATCH THE VIDEO FOR MORE INFORMATION.
KIRO Fill Key Benefits
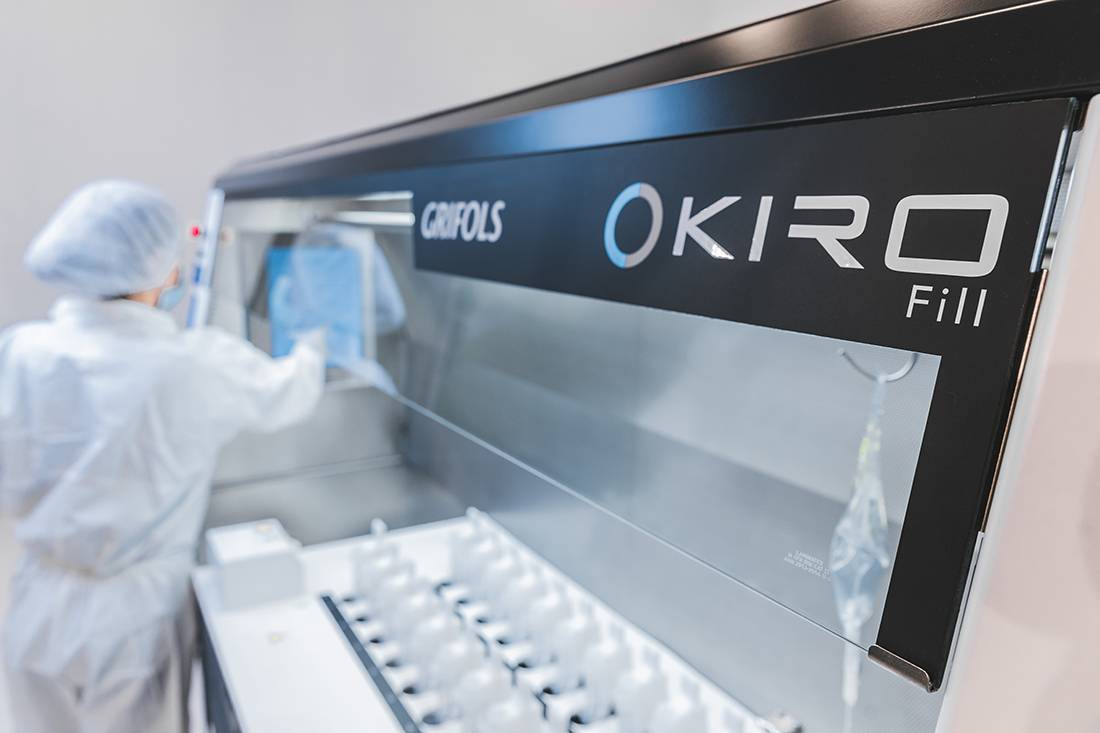
Safety
- ISO 5 aseptic compounding environment protects sterility during production of non-hazardous compounded sterile preparations
- Automation minimizes risk of contamination and increases dosing accuracy
- Repetitive stress and needle-stick injuries are mitigated
- Guided and software-controlled manual loading and unloading of supplies enhance patient safety
Control and Traceability
- Loading and automated compounding processes are controlled by means of barcode scanning and RFID identification
- Batch reports are automatically generated to ensure traceability through production, including environmental monitoring data
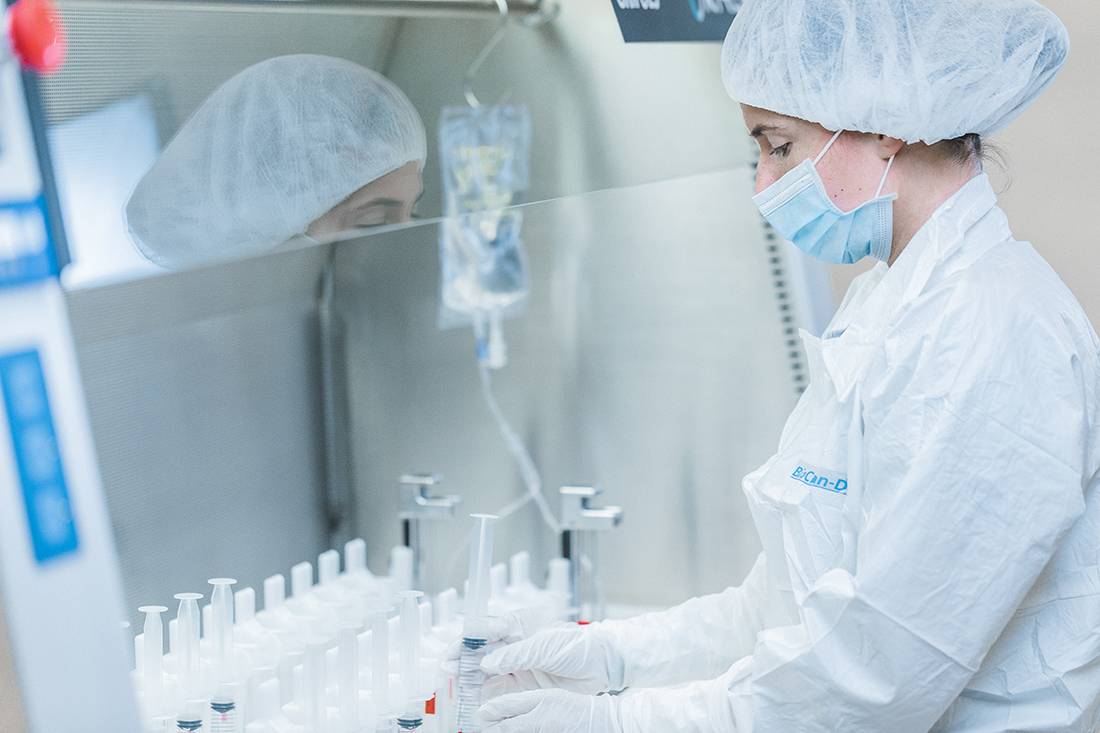
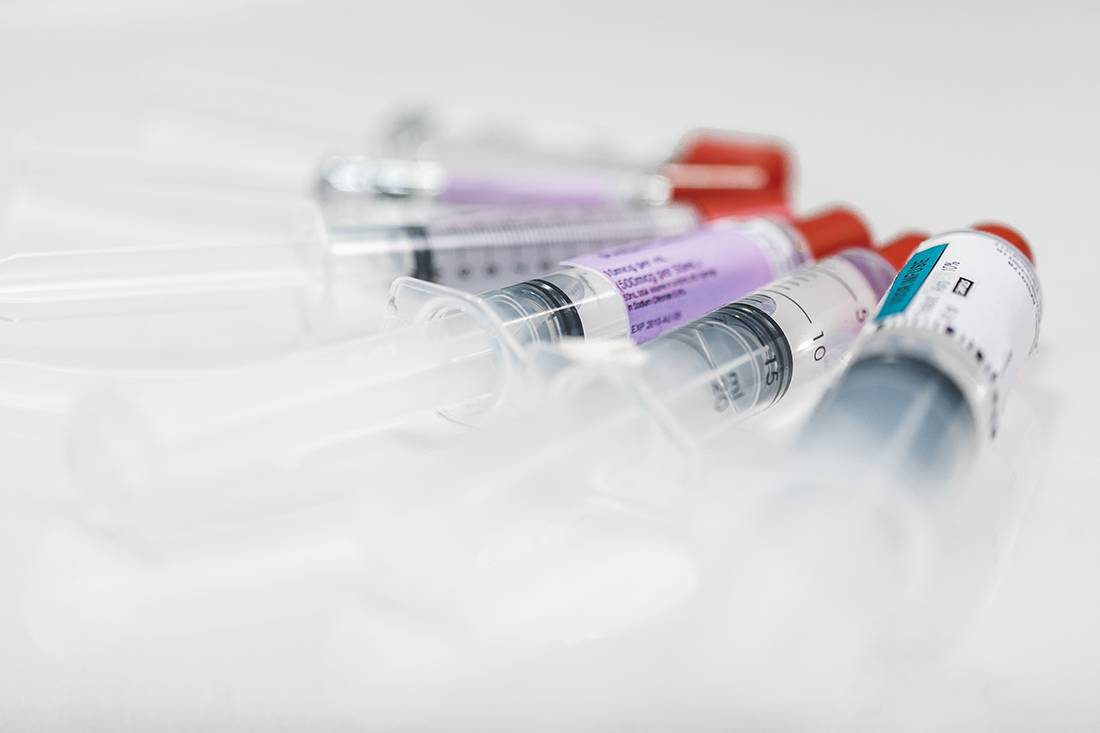
Flexibility and Efficiency
- Unique design and small footprint facilitate high throughput and optimization of workload, workflow, and staff time while consuming minimal valuable cleanroom space
- Integrates two automated units working in parallel
- Accommodates a large variety of sizes and types of source and final containers
- Prepares batch and patient-specific compounded sterile preparations
- Optimizes the use of medication and leftovers
Regulatory Compliance
- Compliance with USP and GMP regulations supported by standardizing aseptic procedures, facilitating personnel and process qualification
- Air flow operation, temperature control, and continuous particle counter to meet GMP requirements
- Fully serviced during deployment, qualification, and periodic maintenance, including dosing accuracy tests and airflow certifications addressing smoke tests under dynamic conditions for USP <797> compliance
- KIRO Fill meets electrical safety requirements by being UL listing marked per IEC61010 and EMC certified per IEC 61326-1
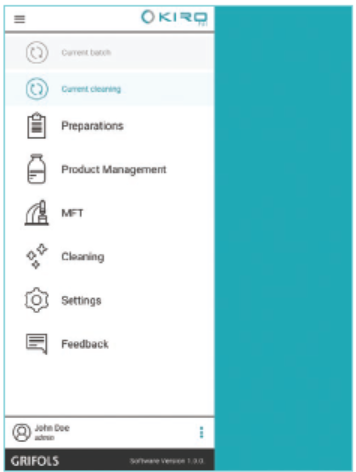
Technical Information
- Size (w x d x h): 81″ x 34″ x 69″ (2055 mm x 870 mm x 1755 mm)
- Minimum clearance (w x d x h): 120″ x 72″ x 80″ (3035 mm x 1820 mm x 2020 mm)
- Weight: 630 kg (1390 lb)
- Required minimum floor load rating: 200 kg/m² (40.9 lbf/ft²)
- Power: 120 VAC ± 10%, 60 Hz, 3 kVA, 14 A in US (230 VAC ± 10%, 50 Hz, 1.6 kVA, 7 A in Europe)
- Electrical safety: UL listing mark per IEC61010 and EMC certification per IEC61326-1
About the Portfolio
inclusiv is a comprehensive IV compounding portfolio of integrated technology, software, and service solutions designed to support your needs for sterile compounding from the design and building of your sterile compounding environment, to the preparation and verification of your products, through the ongoing management and optimization of your pharmacy operation.
For more information, visit www.grifolsinclusiv.com